EPC Scheduling
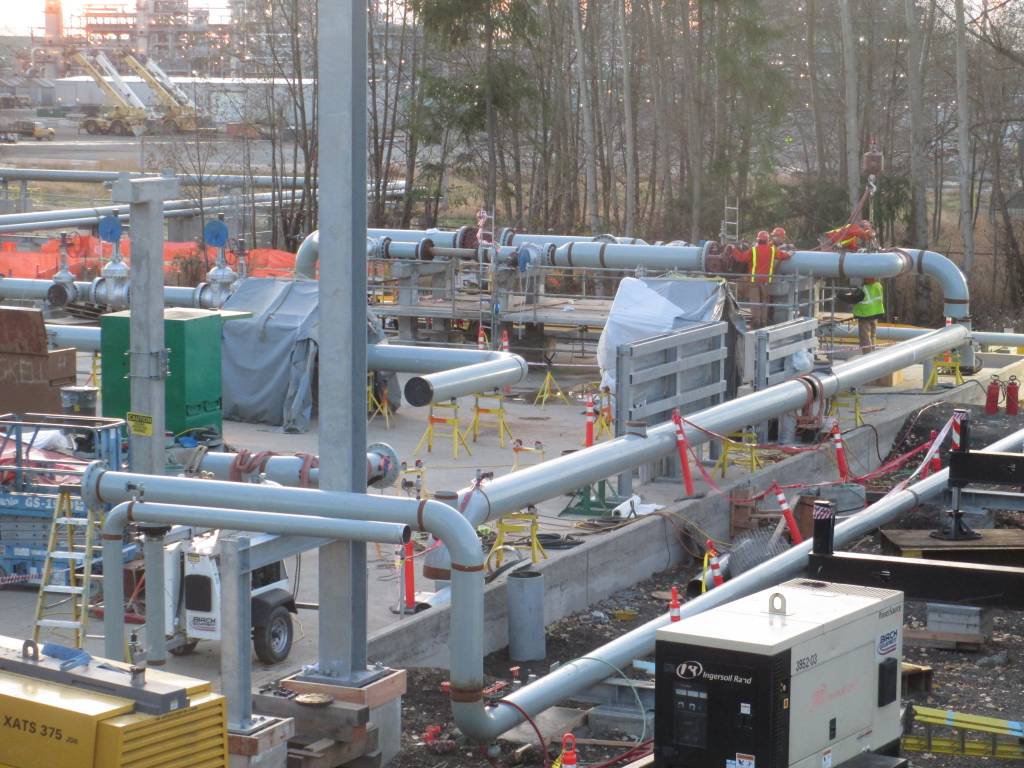
The term EPC refers to the various stages or life cycle of a project. E stands for Engineering; this is where the project is defined, parameters are established, and drawings are produced for Construction to build to. P stands for Procurement; this is where materials are specified, purchased, and manufactured. C stand for Construction; this brings the efforts of the E & P to fruition. This is where the physical construction occurs. There are numerous inputs and outputs that affect the overall schedule throughout the EPC life cycle that you might not be aware of. This document is being written to address some of those items in general terms that can be applied to a vast variety of projects by communicating with your Client.
E-Engineering: Typically, in an EPC schedule, the Engineering portion would cover the various disciplines: Process, Mechanical, Civil/Structural, Electrical, and Instrumentation & Controls. These are not the only disciplines associated with the E in EPC Scheduling. Permitting Efforts (Environmental & Non-Environmental), Survey Work, Geotechnical Work, Land Acquisition, and Public Outreach are additional inputs that drive Engineering tasks. For example, Survey data must be obtained prior to a Site Grading Plan. Geotechnical Data must be obtained in conjunction with information obtained during the Procurement cycle to produce Foundation Plans & Details (amongst other deliverables). This part of the schedule has always shown itself to be dynamic; and what I mean by that is that it can constantly vary. For example, activities can occur out of sequence or activities can be added or deleted based on outcomes of other activities. The key to all of this is to understand the process of how one activity affects another and then how those affect other disciplines. Unless you have worked directly for the Engineering firm, it can be quite cumbersome to understand the various intricacies of the logic surrounding this portion of the schedule. One could assume that because their project falls under a USACE Permit they would have to follow that entire permitting process, but upon further review, an Approved Jurisdictional Determination (AJD) could be issued preventing that entire process from continuing thus affecting your overall schedule. If construction was awaiting the USACE Permit to mobilize, your overall timeline just accelerated. Again, unless you have directly worked for the Engineering firm, the best chance of success is to obtain input from your client. Assuming that this client has had previous success with similar scope(s) of work, they would be the authority in providing key logic as to not only how each discipline’s activity affects itself, but also how they affect the other disciplines. The key takeaway is to make sure that not only is your logic sound amongst its own discipline, but also to make sure the logic is established throughout the entire schedule and all disciplines so that if one activity shifts, the appropriate successor activities do as well. This will prevent major issue from arising, dates being missed or slipping, and confidence being lost in you as a scheduler.
P-Procurement: This portion of the schedule works in conjunction with the Engineering schedule since that is where the actual specification is produced. Once the items are specified, a Request for Quote (RFQ) is produced. Once an item is quoted, reviewed, and a vendor is selected, this is where the procurement schedule then drives Engineering activities. Regarding non-shelf items, there is typically an approval drawing process that must occur prior to manufacturing activities can begin. The approval drawings not only drive the manufacturing process, but they also drive the final design requirements associated with Engineering deliverables. General Arrangement drawings are required for Mechanical designers to properly model the item so Piping Plans and Isometrics can be finalized; GA drawings are also required to finalize structural components; One-lines and power requirements are required to fulfill E/I&C deliverables/schedules as well as some Process deliverables in certain projects. In most cases, schedules do not account for this back-and-forth approval process which ultimately can delay the IFC issuance, manufacturing process, and ultimately the delivery of an item to a Construction Contractor. The cycles vary, and this is where the Client input comes into play. How long do they need to create the specification, how long will they go out for bid, how long will it take for them to evaluate and issue a purchase order, does an item have to be approved prior to specifying another, how long is the manufacturing process? Again, assuming that this client has had previous success with similar scope(s) of work; through the use of historical data, they would be the authority in providing key logic and durations associated with the various procured items associated with a project.
C-Construction: Unlike the Engineering schedule, the Construction schedule is typically linear, and by that, I mean sequential. Activity A must occur prior to Activity B and Activity B must occur prior to Activity C. There are several key steps that will assist you in building the Construction schedule. Those key steps are: Identify the scope, define the logic, determine the sequence, and integration. Typically, during the Engineering Phase, a high-level construction schedule is produced to establish the overall timeline of the schedule. Again, assuming that this client has had previous success with similar scope(s) of work; through the use of historical data, they would be the authority in providing key logic and durations associated with the various construction activities. Once the scope is refined, drawings have been produced, and a Construction Contractor has been selected, this is where the real scheduling effort comes into play. Working in conjunction with the Construction Contractor the scope can be fully defined: setting of equipment, sitework, piping, wiring, foundations, and termination activities. Once the scope is defined we can then establish the logic: sitework must occur prior to the foundations. Foundations must be set prior to setting equipment. Equipment must be set to run piping and connections to the equipment can be made. The equipment must be set before you can run wire and terminate. Once the logic has been established, then we can sequence the activities. The procurement schedule will help sequence the major equipment; you cannot set a piece of equipment until the manufacturing is complete and the item has been delivered to the site. Using a Compressor Station as an example; working inside the building, typically, we try to work from the inside out. This will prevent you from “boxing” yourself in. In conjunction with sequencing comes the integration. What systems are required for startup and when? If multiple commissioning activities are warranted, you might sequence the schedule to accommodate the Client’s commissioning schedule.
There are numerous detailed discussions that can be had among a variety of topics addressed in the write-up. Again, this just speaks to the EPC schedule creation in general. The purpose of this is to endorse and encourage communications with your client to help you produce a more accurate schedule.