Last January, news of the latest coronavirus began to increase in volume. The numbers in China were following the forecasted exponential growth rates, which I equated to bad news for the USA. Telling my wife to stock up for the pandemic was a tough Saturday conversation when the plane was leaving for Mexico Monday morning. Instead, I came home March 12th, and only yesterday were we able to buy toilet paper. #humblebrag
Now that I’m not worried about TP, I can worry about construction. Losses will be spread throughout our industry, from executives to field day labors. It’s bad enough to have less people, but the COVID-19 loses will be concentrated in the statesmen/elders’ bracket. In the field, our senior craftsmen, the backbone of our industry’s production knowledge base, is also the highest at-risk. So not only will the craftsmen decline continue, but our losses will be concentrated in our highest producing group. Some lost will be leaders in a larger company or trade, others will be smaller specialty contractors. We’ve got some tough conversations coming between owners and contractors.
Productivity is going to suffer. The folks we lose are going to take precious knowledge. Those left standing might realize their immortality a decade early. Safety awareness will increase. Even though some work requires close quarters, in general, we’ll be looking for ways to spread out a little more. Coming into and out of the work front, Hygiene will take a bit longer. Along with losing efficiency, we’re going to have less people, and they will require more “distance” to do the work.
All of these arguments sound like reasonable justification for productivity declines. Few could debate the basis of the impact. Fewer will pay for it, because it’s difficult to measure. Talking about production deficiencies is one thing, measuring and modeling it is another. But how? Resource leveling. Scheduling software and CPM schedules should not only provide critical path calculations, but should also be able to generate different scenarios through resource leveling.
You’re probably familiar with how resource loaded schedules are used:
- Head counts-most common application of a “resource loaded schedule”
- Cash-flow and Schedule of values-after assigning a value to each task, the value of work completed can be shown over time, invoices can be based upon the earned value
- Key-Quantity-on large jobs, commodity production becomes the bottle neck when numerous work fronts are available. Or, in lump sum environments, counting the widgets is the best controls available.
At HITO, we’ve gone a step further:
- Megawatts of power required for start-up of each system.
- Density tracking-how many craftsmen are planned for each area.
With HITO’s help, we can help you measure, model, and manage the impact of each risk area:
- Production: Do we have the headcounts expected to produce per the plan? If we only have 50 pipefitters available, what is the impact on the finish date? If we slow concrete production to 250 m3/week, will the concrete be cured for the first major OEM delivery?
- Productivity: Are we able to produce as efficiently as planned? If production is 90% as efficient as planned, how many more craftsmen will need to be added to offset the deficiency? If is the impact of working Sunday? When can we start pulling from the firing line to man-up the tie-in crews? My joke with electricians: What’s the latest you can start a night shift and make up for the pipefitters?
- Density: What impact will limiting access to areas have? Are crew sizes limited? If we can only fit 5 electricians in the electrical room, how many days to terminate controls, taking into account the device side pull and termination.
Most schedulers don’t get past the first point above. With our diverse experience, HITO can help your team by taking it to the next two steps. The third method, density management, is probably the most unique item to model, yet proves to be the bottleneck in many projects.
Not only can we mathematically model density management, we have also shared it graphically in our easy to read FlipBook format. We used a grid approach of a refinery’s FCC unit.
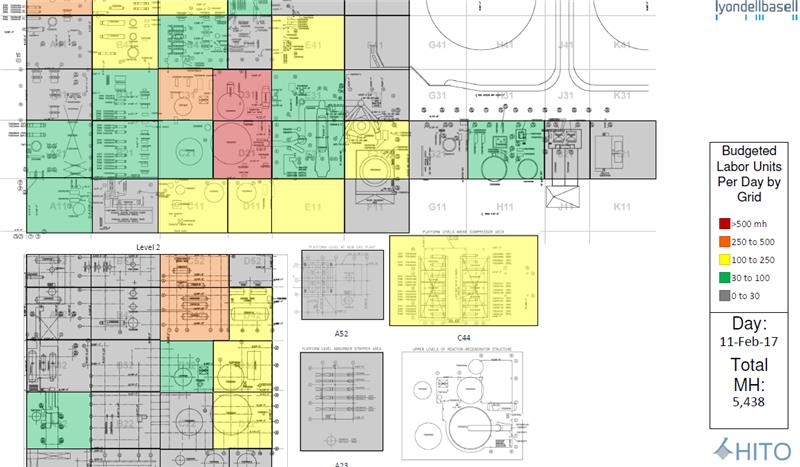
The color of each grid is determined by the hours planned for each shift. The second use of it was requisitioned by the safety department.
Your family, friends, company, and clients will suffer. Projects and companies will be impacted. In order to do it safer, we need to know its impact, adjust our models, and tune-up our expectations going forward. Talk to the company on the other side of the contract. It’s a tough conversation, but have the it while the toilet paper is on the shelf.